Application requirements of RFID inventory equipment in manufacturing
Source:Powered | Author:admin | Time:2022-07-18 | Views:1270
The manufacturing production line consumes a large amount of materials almost every month due to procedures and management, and the production results and expectations are affected by errors from time to time, and the production line often causes various errors due to human reasons. With the help of RFID technology, a highly organized and integrated control system can be formed in the entire production process, which can realize the identification and tracking of raw materials, parts, semi-finished products and final products in the entire production process, reducing the cost of manual identification and he error rate to ensure that the production line is balanced and coordinated.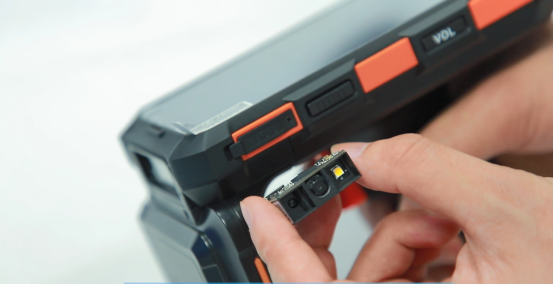
Sticking RFID tags on production materials or products can automatically record production information such as product quantity, specification, quality, time, and person in charge, instead of traditional manual records; the production supervisor can read product information at any time through the reader; other related Personnel can grasp the production status in a timely manner and adjust the production arrangement according to the situation; purchasing, production, and warehousing information are consistent and can be monitored in real time; before materials and products leave the warehouse, the system will automatically record the inbound and outbound information, and can track the location of the items in real time.
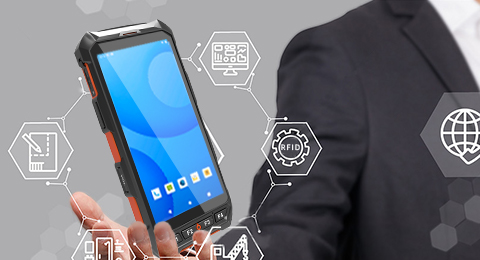
Application Features of RFID in manufacturing:
1) Real-time data sharing
Install RFID inventory equipment in each process of the production line, and place RFID tags that can be read and written repeatedly on products or trays. In this way, when the product passes through these nodes, the RFID reading and writing equipment can read the information in the label on the product or the pallet, and feed this information back to the management system in the background in real time, so that the manager can keep abreast of the working status of the production line. .
2) Standardized production control
RFID systems can provide continuously updated real-time data streams, complementary to manufacturing execution systems, and the information provided by RFID can be used to ensure the correct use of machinery, tools, and parts, thereby enabling paperless information transfer and reducing downtime. Going a step further, as raw materials, components and assemblies pass through the production line, the production process can be controlled, modified or even restructured in real time to ensure production reliability and high quality.
3) Quality Tracking and Traceability
On a production line where RFID systems are implemented, product quality is checked by a number of test positions distributed in several locations. At the end of production or before product acceptance, the quality of the part must be clearly expressed with all previously collected data on the part. This can be done easily with RFID tags, because the quality data obtained throughout the production process has already gone down the production line with the product.
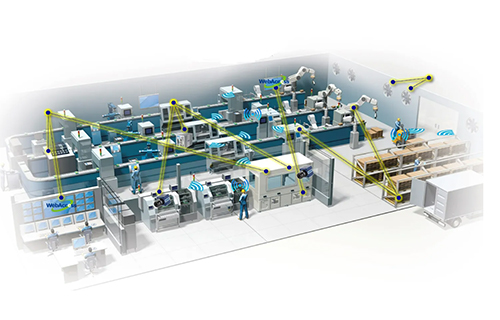
System functions that can be realized by RFID:
According to the requirements of the overall design of the manufacturing system, the entire RFID application system includes system management, production operation management, production query management, resource management, production monitoring management and data interface. The functions of each main module are as follows:
a. System management.
The system management module can define the production characteristics of a certain type of product and the users of the management information system, the authority to perform functions and the authorization of users to use the functions, complete the data backup operation, and maintain the basic data common to each subsystem, such as process (bit) , workers, workshops and other information, these basic data are the functional basis for online settings and operation scheduling.
b. Production operation management.
The module accepts the master production plan rollingly, automatically generates workshop for intuitive reflection, and provides decision-making basis for managers. The query function can query the operation information of each station, such as the specific time of assembly, material demand information, employee operation results, quality status, etc., and can also trace the production history, so as to locate the links and causes of defective products.
c. Resource management.
This module mainly manages some equipment required by the production line, provides the user with the current working status of each equipment, and timely understands the actual use of the existing equipment, so as to provide a reference for arranging production or equipment maintenance, according to the load of the production equipment. Develop daily, weekly and monthly production plans for production lines to ensure normal production.
e. Production monitoring and management.
This module mainly provides information to general users, enterprise managers, leaders and other personnel who need to know the production progress in time. It mainly includes real-time monitoring of order execution, real-time monitoring of process production, and real-time detection of station (station) production. These real-time monitoring functions provide users with overall or partial production execution information, so that users can adjust production plans in a timely manner according to actual conditions.
f. Data interface.
This module provides data interface functions with workshop electrical control equipment, IVIES, ERP, SCM or other workshop management information systems.
With the help of RFID technology and related RFID intelligent terminal equipment, labels, etc., real-time data collection visualization, punctuality, business collaboration and product information traceability in the production process can be realized. The RFID system is seamlessly integrated with the automation system and enterprise information system to build a supply chain-oriented RFID architecture system, so as to realize the sharing of product information in the supply chain, and fully realize cost reduction and efficiency increase.
Contact Us:
If you want to know more information? Please fill in the following message form, we will contact you in the first time.
Copyright 2019 - 2024 Shenzhen Rakinda Technologies Co., Ltd. All Rights Reserved www.rakinda.com Privacy Policy